When Digitalizing Lean, Start with Removing Information-related Waste
In 1948, when Taichi Ono and Eiji Toyoda set out to design the Toyota Production System (TPS), they chose to empower the workers on the factory floor to create a “living and learning” system that was people-centric. It was a radical idea back when factory workers were seen as “doers” and not valued as “thinkers”. The resulting Lean philosophy which emerged was based on people at the center of an adaptive and flexible system that was continuously improving and innovating.
Any effort to successfully digitalize Lean must enable and build upon these core principles. To ensure this objective, AVEVA worked closely with Schneider Electric to get input from over 40 experienced Lean and Supply Chain practitioners to design and develop a world-class solution.
The resulting Discrete Lean Management (DLM) solution does just that.
As illustrated below, it builds upon the Lean foundation already created through changes to mindset, culture and processes (which helped make Schneider Electric the 4th best-run global supply chain in 2020, ranked by Gartner), and focuses on the additional value by removing the waste or losses related to information management activities.
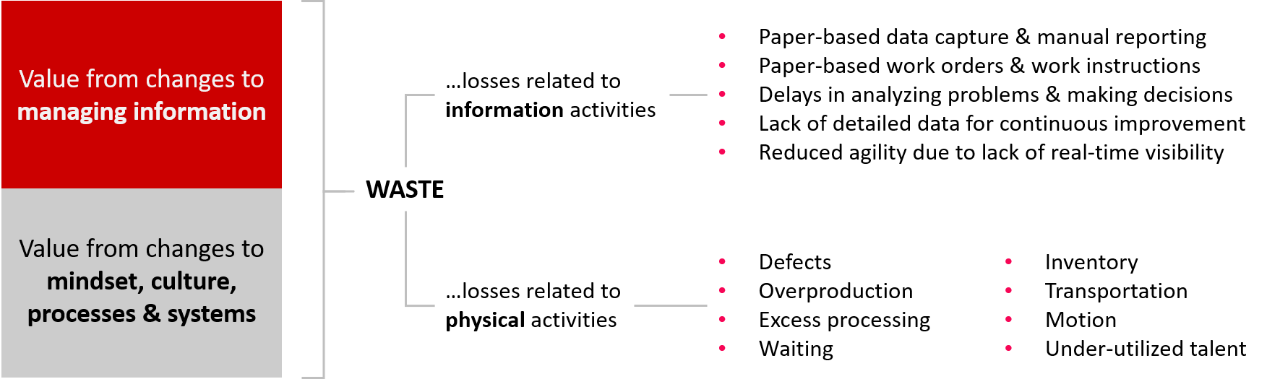
Two key takeaways worth highlighting:
1. The successful rollout of the Discrete Lean Management solution across 70 Schneider Electric manufacturing sites proves that digitalizing Lean can be done right without compromising its core design principles. (Click here to read the success story.)
2. Discrete Lean Management helps get started by removing information waste. It lays the foundation upon which further digitalization can be added to the Lean journey. According to independent studies, fully embracing digital tools can double the value from Lean efforts, as illustrated below. (Click here to read the whitepaper)
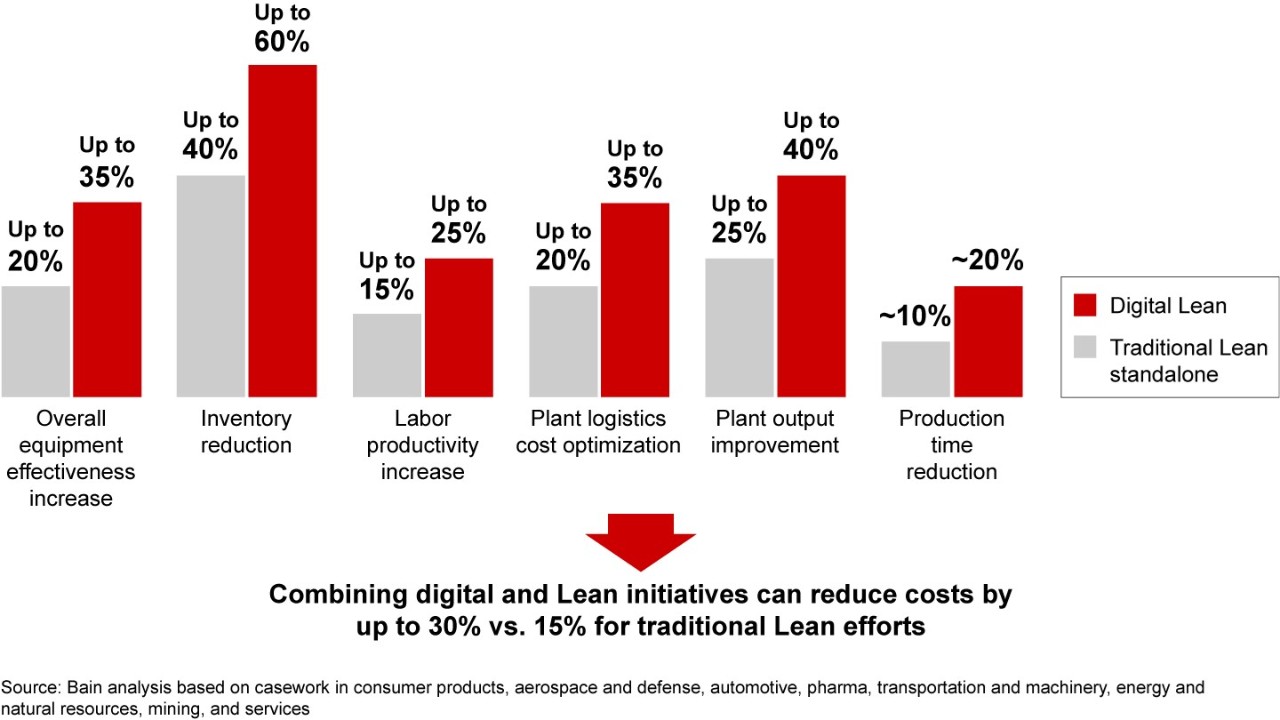