Uncovering Opportunities Using Process Data
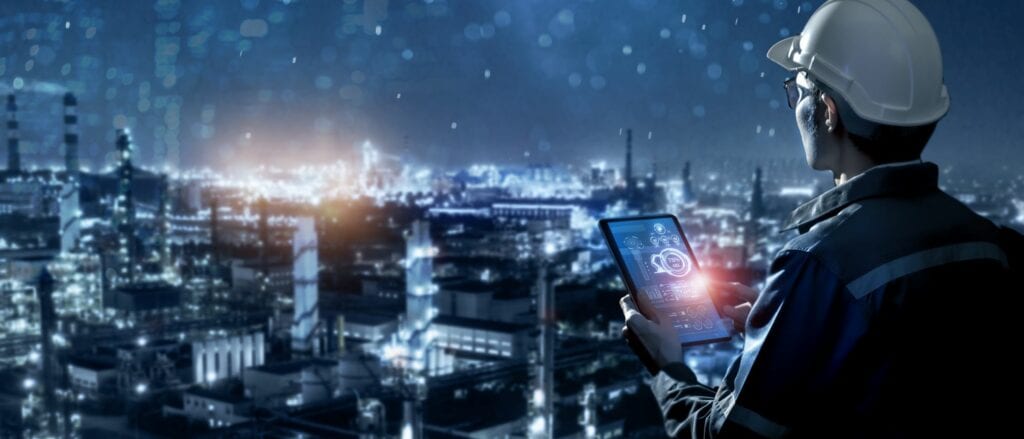
Written by Jeremy Wilbert, Sr. Product Marketing Manager, AVEVA
Examination of process data and alarms—contextually logged using historian software—is important to understanding problems and uncovering opportunities.
The previous blog in this series, Empowering Industrial Troubleshooting, described how contextual and accessible data empowers troubleshooting of industrial manufacturing and processing operations. This third and final blog focuses on transforming raw process data into meaningful insights, usable throughout an organization so people can make informed and timely decisions, improve operational efficiency, and reduce costs.
We have all heard the phrase about someone “who can’t see the forest for the trees”. For industrial operating companies, think of all the raw process data as the trees—or maybe the leaves and needles. To gain certain useful information about the layout of the forest, a perspective derived from a higher vantage point is necessary.
In addition to traditional automation data, it is now quite cost-effective to obtain many types of measurements from other IIoT sources, resulting in accelerating the growth of the amount of available big data. The challenge is discerning which data actually impacts outcomes. Digital data systems are the primary way for operating companies to track performance and discover how they can act to improve production efficiency, minimize energy consumption, reduce waste, and verify compliance.
Transforming Data into Insights
Processes must be measured to be managed, but simply recording the raw data is not enough. Analysts need the tools to process data and create real-time and summary key performance indicator (KPI) metrics such as overall equipment effectiveness (OEE) and other calculations describing production operation and assets. Data analysis software makes it possible for users with process knowledge to perform these investigations easily, alleviating the need for advanced programming skills.
Analyzing real-time and historical data, these calculations allow teams to define performance for the current and past periods with quantifiable metrics. In many cases, trending performance can predict impending issues, and as these are identified, the team can work on discovering their root causes and solving the problems. From a proactive standpoint, analyzing operations over time can uncover opportunities, prompting users to test new operational methods or parameters. As changes are implemented, it becomes possible to document results.
Democratized Access Empowers Workers
Results must be effectively shared to be useful, but static or incomprehensible displays are of limited organizational benefit. Instead, designers need options for arranging the information into various formats suitable for multiple audiences, and for distributing these outputs wherever workers are located.
More than ever, workers are geographically dispersed, and certain specialists may support many locations. Some end users simply need high-level dashboards, while others require detailed reports or data dumps for further analysis.
Reporting software and platforms make it possible for designers to configure information presentation in multiple formats, and deploy it as needed. Certain dashboards are required for control room big screens, while others are embedded in emails, and still more are accessible as web-hosted reports on an individual user’s mobile device. Software advancements empower designers to customize multiple formats to better serve all users.
Calculate and Communicate
Modern historian and analytical software can be deployed on-premises, in the cloud, or in a combination of these locations, helping end users access critical operational data, transform it into valuable insights, and communicate the results to the workers who need it. With the right platform, any company can position themselves to discover and take advantage of formerly hidden opportunities.