The Drive for Practical Data Management
Written by Jeremy Wilbert, Sr. Product Marketing Manager, AVEVA
Historian software helps sites capture data so they can analyze the most efficient ways to operate.
The next time you board an airplane, consider for a moment the pilots up front charged with getting you safely to the destination. Would you prefer for them to operate entirely by the “seat of their pants”, or would you like for them to receive relevant data, presented to them clearly, to help with the task? The latter is obviously preferable, and airline technology has evolved to manage the data accordingly.
However, for many manufacturing and process companies, trusted and timely data can be hard to come by. Yet high-quality information is required for the accurate decision-making which leads to improved performance, safety, and reliability. Many companies have taken some steps toward digital transformation as it has become easier to connect with the data generated by people, devices, and processes, but many still rely too heavily on less-effective tools like spreadsheets.
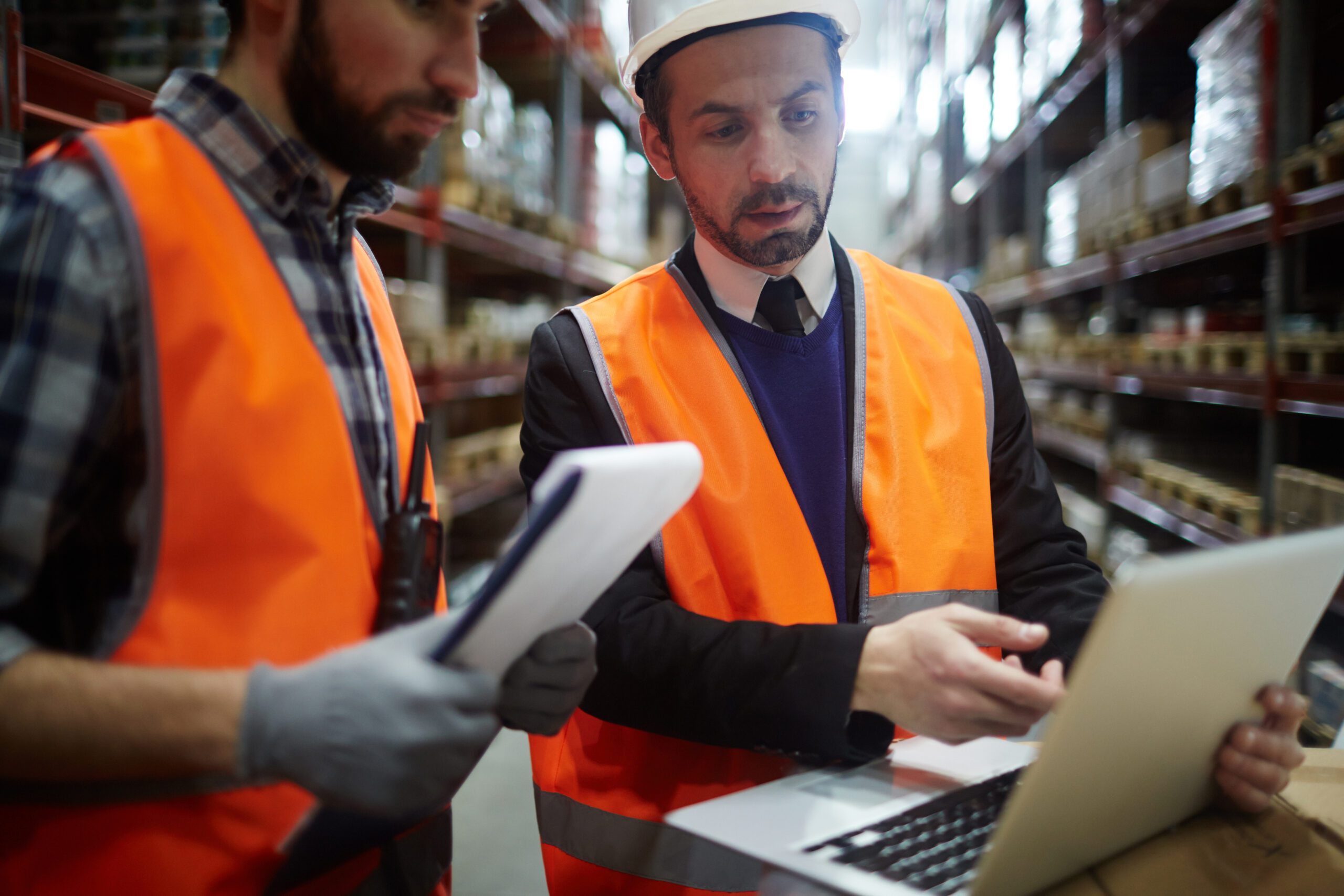
Spreadsheets are not going away, but neither are they the best tool for deeper analyses or recordkeeping. This is partly due to the ever-increasing volume of industrial internet of things (IIoT) big data, which multiple studies and surveys show is exceeding the ability of companies for effective management and analysis. Operational information management is also about more than collecting and storing data, as it includes consolidating large volumes of data and contextualizing it so users can tap into its value.
To improve the situation, operational end users need practical ways to capture and consolidate data, so they can:
- Reduce unplanned downtime, by acting on automatically collected condition monitoring.
- Improve asset utilization, by evaluating equipment availability and efficiency.
- Increase production and quality, by analyzing operational data to determine optimal running parameters.
- Ensure regulatory compliance, by producing reports of operating history.
A historian is the software needed to perform these tasks by bridging the gap between manufacturing site operational technology (OT) equipment and the information technology (IT) based enterprise systems.
Capture
Paper-based or manual processes and procedures are labor-intensive, error-prone, and rarely optimal. Even with automated connectivity to varied sources like traditional industrial automation systems, IIoT smart sensors, energy monitoring, and other forms of instrumentation—it is all too easy for data to remain isolated in silos and lacking in context—and therefore useless for quickly generating correct recommendations.
Implementing an industrial historian is the first step to accessing operational data and connecting the edge to the enterprise. Automating data capture is the only way to obtain and store high-fidelity, accurate, and timely data for ready access across the organization. A capable process historian or a cloud-based platform consolidates all data sources to simplify data consumption, reporting, and analysis.
It is important to note that an effective historian should be able to be scaled up as needed over time. Use cases may not immediately be obvious, so it can be important to store many types of potentially relevant available data, which may lead to useful inferences in the future. Or, new data candidates can be added as it makes sense.
Compute
Once the supervisory historian is in place and bridging OT and IT systems for data capture and consolidation, analytical efforts can commence. Uncovering subtle but meaningful patterns can be tricky. It can be difficult to understand how to apply insights so day-to-day operations can properly be harmonized to maximize return on investment (ROI).
This is where manufacturing intelligence software shines by bringing all of the corporation’s operations-related data together for analysis. Manufacturing intelligence software is designed to automate the extraction and transformation of this data, delivering:
New structure improving data interpretation
- User-friendly analytics
- Key performance indicators (KPIs)
- Other metrics
- Dashboard-based monitoring
- Visual summaries
- Reports
Working in near-real-time, manufacturing intelligence software reveals a single version of truth across all plants and the enterprise. This provides users with new tools to evaluate specific production goals on various machines or at multiple sites, perhaps in conjunction with energy consumption or equipment performance capabilities.
Enterprise Digital Transformation
Operating a company by gut feel or intuition is no longer a viable option, especially considering that industrial historian and manufacturing intelligence software is available to help any company with their digital transformation efforts. Historian and manufacturing intelligence software are foundational for progressing any manufacturing company to greater efficiencies.