Sustainable, efficient net-new plants: Three questions to ask before commencing your next greenfield project
Written by Julien de Beer, Head of Portfolio Management, AVEVA
Our industrial world is changing – fast. Designing and operating efficient plants remains paramount, but environmental targets are no longer nice-to-have aspirations. Meeting Environmental, Sustainability, and Governance (ESG) goals is now central to securing funding, gaining regulatory approval to operate, and protecting brand reputation.
To navigate the energy transition and remain competitive in the future, industrial leaders are making massive greenfield capital project investments in Net Zero, carbon capture, utilization and storage (CCUS), hydrogen production, and renewable power generation facilities. Unlike their more traditional predecessors, these facilities will be designed from the get go as fully digital, connected plants that can be easily updated and modernized for many years into the future.
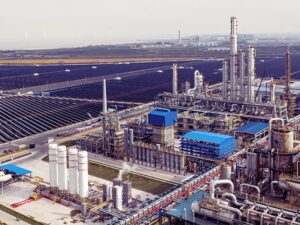
The connected plant future is nearly here. Are you ready?
Visit our Engineering the Plant of the Future page to discover how your plants can meet the future with innovation, flexibility and resilience.
The need to execute projects and operate leaner and greener plants is transforming every aspect of plant design and operations. Digital workflows are being adopted widely by industrial leaders like Wood and Shell to enable automation and streamline collaboration right from the earliest design phases of greenfield capital projects through to operational excellence.
Three questions to ask before you get started: What, how, and when?
Engineering a future-proofed industrial plant is no easy task. There are three key questions that every Owner Operator and their Engineering, Procurement, and Construction contractors (EPCs) should ask before embarking on their next capital project.
1. What can we do to better connect our people, processes, and decision making?
Sustainability isn’t only about reducing environmental impact, it’s also about finding smarter ways of working that transform performance.
Two of the biggest hurdles in capital project delivery are siloed working and weak project control and oversight. Furthermore, owners understand the long-term value of digital twins, but are often challenged to piece together the necessary engineering and operational data required to form them post-handover.
A unified approach to engineering and execution on the cloud aligns everyone around a single hub of verified data in the project phase while contributing to the core of the digital twin that can be handed over at the end of the project. Engineers work better together, sharing ideas and knowledge across disciplines. Risks of design changes are flagged and dealt with early to reduce risk of cost overages and delays, and time is freed up for innovating to identify better processes and design solutions that can be repeated from project to project.
The data-centric approach to design, facilitated by the digital twin also significantly improves handover with a complete representation of all 1D, 2D, and 3D data transferred from EPC to Owner Operator. This holistic digital twin approach unlocks instant value by informing the project delivery process itself, and can be leveraged to empower operations to provide lasting value for years to come.
2. How can project teams leverage digital transformation to achieve their sustainability goals?
Digital twin technology provides the control, visibility, and insights to create a plant of the future that delivers on ESG goals while driving performance throughout both the project and far beyond start-up.
With greater transparency throughout all project stages, wasted resources and materials can be minimized. Process simulation can quantify future plant emissions long before the process design is set, ensuring the plant will meet its environmental requirements. And, once fully built, sensors will connect into the digital twin to gather real-time data to identify opportunities to further reduce the plant’s carbon footprint and optimize future maintenance and even new plant designs via the digital thread
The digital twin is at the core of these data-driven capabilities, deriving tangible value at all points throughout the process.
3. The Industrial sector is still recovering from a challenging year, when is the right time to make this change?
The short answer is now. Owner Operators and EPCs around the world are already embracing digital solutions – a trend that has accelerated fivefold since the start of the pandemic. With increasing global competition, new regulatory requirements and constant financial pressures, organizations across the industrial spectrum are doubling down on digital transformation efforts to pave the path to a more resilient future.
Worley joined forces with AVEVA in a transformational enterprise-wide software partnership in 2019 to simultaneously improve business resilience and project performance. The partnership provided flexible, cloud and subscription-based access to AVEVA’s entire engineering portfolio and meant more than 180 of their projects could remain in motion despite worldwide remote working during the pandemic.
Elsewhere, Veolia Water Technologies turned to AVEVA to align its engineering teams, enhance operational efficiency, and contribute to its sustainability goals. The move has standardized engineering processes across 260 locations globally, while the transition from on-premise to the cloud also freed up 20% in IT agility.
Meanwhile, it was estimated that by the end of 2020, 67% of enterprise infrastructure would be cloud-based. By now it’s clear, when it comes to digital value that the sooner you start, the more you benefit. If your organization hasn’t started on your digital twin journey today, now is the time to get going, and AVEVA can help.