Plotting Your Automation Maturity Position from Reactive to Proactive
As global companies adopt and leverage digital transformation, they are implementing smart systems and adding connectivity to data sources to improve their operations and empower their workforce. Whether they are food and beverage suppliers, water treatment facilities, machine builders, or manufacturers of any kind, these organizations are realizing competitive advantages such as:
- Increased operator productivity and efficiency.
- Improved connectivity between enterprise and industrial automation software.
- Newfound operational agility to adapt and scale.
- A workforce enabled with process improvement tools at their fingertips.
- Clarity and sustainability driven by enterprise standardization of products and processes.
- Availability of always-on IIoT data for review and analysis from anywhere.
But while these benefits add value, the next steps to take on the digital transformation journey may be a bit foggy, delaying adoption. Adding to the challenge, the best moves rarely involve a one-size-fits-all solution. Each organization must instead incorporate and accommodate their unique systems and operational needs using a wide range of available technologies.
This process can be aided when a company evaluates and determines their current ‘automation maturity’ position, offering insight on gaps in information or capabilities. Throughout this blog series, we will examine five positions in the automation maturity journey. To find out where you and your organization stand and how to improve your automation maturity adoption, take our complimentary Automation Maturity Assessment.
Reactive Hurdles
Do you find your organization losing time and efficiency due to a lack of automated processes? Are information gathering by hand and ad-hoc paper reporting common practices? If either of these scenarios resonate with you, your organization may be in the earliest stage of automation maturity, and ready to begin the journey to improved operations.
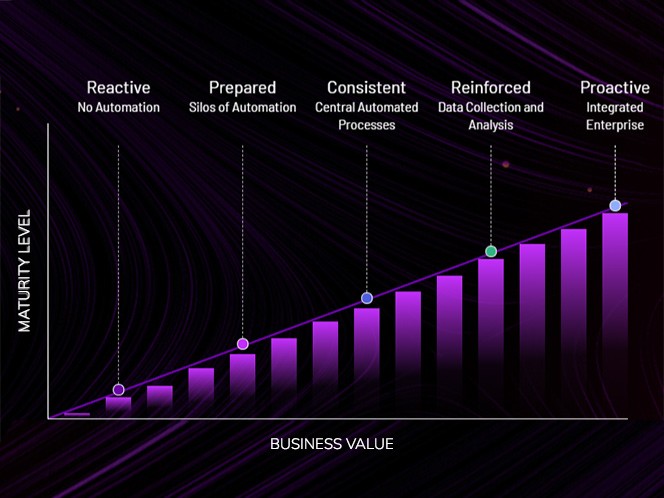
At this reactive level, organizations are prone to mistakes and unplanned production downtime, factors reducing profitability and risking company reputation. In such cases, it is difficult to predict and plan the enterprise trajectory because control mechanisms are few and far between, and ultimately a scattershot strategy rules the day.
In this type of setting, often lacking a clear corporate vision, it is challenging to coordinate effectively with coworkers because goals are poorly defined and targets may shift day-to-day. Open communication and well-defined direction are essential to creating productive collaboration, and this is difficult to produce in uncontrolled environments.
Additionally, there is likely little—if any—automation of work processes, adding to the likelihood of mistakes and inconsistencies. Automation can help cut down on errors and also standardize service, product, and process delivery, making forecasting more accurate.
Operational Deficiencies
On the operations side of the house, reactive organizations have a hard time planning and optimizing production because they are constantly striving to avoid crises, and operational decision-making is limited by a lack of visibility. To gather necessary information for controlling and resolving issues, field technicians make frequent site visits because little or no device status and equipment health is transmitted to the control room.
The plight is aggravated by old technology with vendor-dependent communication drivers, distributed across an enterprise’s control systems. Supporting multiple platforms from several vendors—each tied to a unique system—is inefficient and inhibits operational agility, and unpatched device firmware and software applications pose security risks.
Without edge to enterprise Industry 4.0 fundamentals in place, organizations cannot prepare for the challenges confronting them, instead stepping blindly ahead and hoping for the best. Some days this works, but it often results in negative outcomes.
Where to go from here?
If you find your organization at the reactive stage, it simply indicates a great opportunity. There are large, noticeable gains to be made in efficiency and reliability at this stage with only a few adjustments. AVEVA can assist in your quest to improve process visibility, reduce paper clutter, and access data remotely through technology modernization.
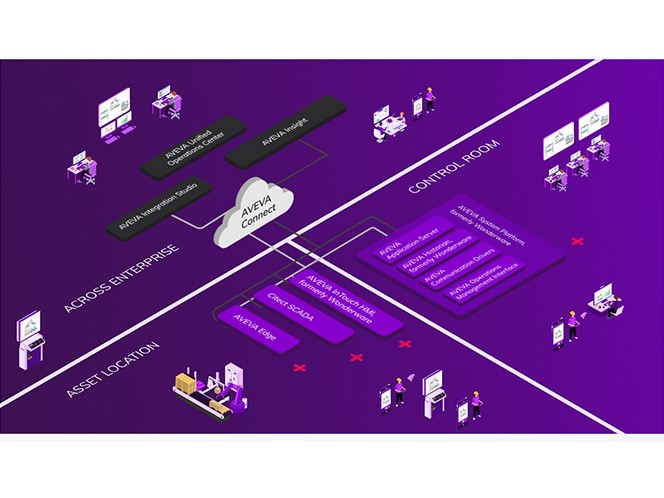