No one likes surprises: Predictive analytics turns them into gifts
Written by Petra Nieuwenhuizen, Product Marketing Manager – APM, AVEVA
Surprises are rarely a good thing, especially when it comes to plant operations. Many industry leaders are realizing the potential gains that predictive analytics can bring to their organizations. The ability to detect asset anomalies and predict future incidents drives production optimization, minimizes downtime, and generates significant cost savings.
AVEVA’s customers have saved millions of dollars as the result of a single detection. Imagine how that impact was multiplied when they scaled their predictive analytics to achieve greater overall equipment effectiveness (OEE).
To maximize your OEE you’ll have to look beyond simply optimizing availability and expand to optimizing your quality and performance. Process analytics like predictive quality, predictive throughput, and predictive energy efficiency help maximize cost efficiency in production processes. Let’s take a deeper dive into these solutions.
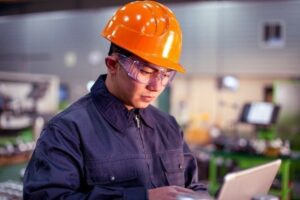
Increase Overall Equipment Effectiveness and connect your workforce with a digital thread infused with Artificial Intelligence.
Predicting quality to minimize waste
How many of you deal with scrap from frequent line startups and formulation changes? We all know that quality testing can lead to lag between the key unit operations and the finished product, as well as scrap generated due to quality adjustments.
Wouldn’t it be great if you could systematically optimize quality over the short and long term, shorten testing, and minimize scrap?
Some organizations look to AI and machine learning to solve these problems. These tools allow plants to predict quality parameters where there is no real-time measurement available or generate a prediction more quickly than offline measurement allows — essentially using an offline lab test to predict a quality parameter before a production process is finished.
AVEVA Insight uses advanced analytics, where inputs can include a variety of process measurements (density and moisture, for example) and product characteristics (such as recipe parameters) that come from different stages of the production process. This means you can measure the quality of your product at any time during the production process and act accordingly if quality parameters deviate.
Operators receive alerts and messages on quality deviations and can view results in dashboards that are customized to display variables like ideal condition values and anomaly breakdowns, depending on an organization’s needs. It’s not hard to see how these changes can reduce waste and shorten the time needed for quality testing.
Predicting energy efficiency to ensure sustainability
Many organizations have sustainability targets and are always looking for ways to make production processes more environmentally friendly. Utilizing predictive energy efficiency is one way to meet those sustainability key performance indicators quickly and efficiently.
Simply put, the goal of predictive models and advanced analytics is to find the best operating conditions to minimize energy consumption during production, plus identify procedures that minimize energy consumption while assets are not running.
Specified models can analyze thousands of process variables in real-time to identify patterns and conditions that allow you to operate in the lowest possible energy state. The models also provide insight into predicted versus actual energy use, as well as the optimal energy use for your specific product, unit, or plant.
After implementing AI and machine learning, a large consumer products manufacturer reduced its global manufacturing energy footprint by 5% across all utilities, including water, air, gas, electricity and steam within one year!
Predicting throughput for optimal process conditions
Process throughput measures how much of a completed product is delivered within a given period. The more production time is shortened, the more an organization can increase efficiency and realize cost savings.
AI and machine learning allow for throughput optimization on products and lines. Models can leverage thousands of process variables and generate the patterns and conditions that allow you to operate at the highest possible production rate. Operators receive alerts with recommendations for action, and engineers can take a high-level look at the best operating conditions to maximize production. Operations data is stored in the cloud, providing quick and easy access to both real-time and historical information.
The cloud can accelerate success
AI and machine learning really shine when they are embedded into a closed-loop process in the cloud, giving you both historical and real-time data, as well as mitigating actions and value chain optimization in one place. This cohesion enables your workers to drive safe and reliable operations by increasing overall equipment effectiveness, reducing unplanned downtime, and building the confidence to shape a sustainable future.
Unplanned events are always going to be part of operations, but we can reduce them. Think of AI and machine learning as the wrapping paper to transform your surprises into a positive gift. Adding prescriptive guidance to your analytics allows you to act immediately — it’s the perfect bow to make you (almost) want surprises in your operations.
The future is clear
Whether it’s saving money, increasing sustainability, or enhancing throughput, AI and machine learning can help your organization take OEE to the next level. AVEVA’s customers have increased OEE by fifteen percent, saved up to thirty percent in maintenance costs, reduced downtime by twenty five percent, and increased workforce efficiency by twenty five percent.