Meet the industry principal: From steel-toe boots to digital twins
Written by Stephen Reynolds, Industry Principal for Chemicals, AVEVA
At AVEVA, we provide the tools and applications that help our customers manage their plant and business data through every phase of an asset’s lifecycle, from inception and design to operation, maintenance, and optimization. Having the right information throughout that asset lifecycle is critical to empowering the right people to make the right decisions at the right time. This series will talk through each piece of that puzzle, and will include blogs that cover the following themes:
- Design and build
- Training
- Operate and maintain
- Optimization
- Change management
- Sustainability
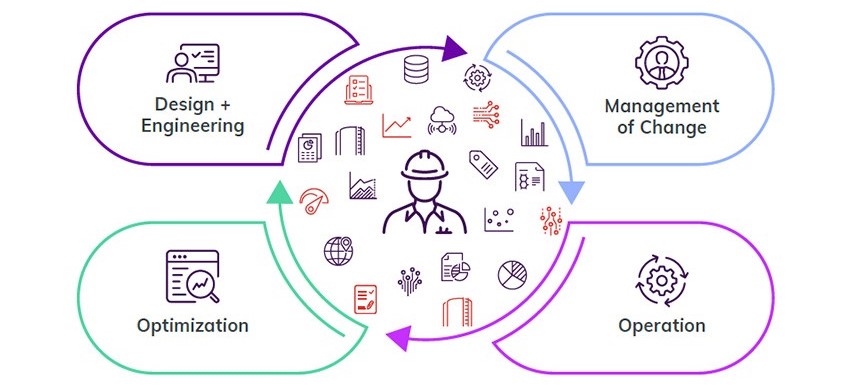
For this first installment, I’ll discuss the design and build phase. It’s important to recognize that, while each of these bullets is important on its own, it is difficult to separate one from the whole; each element enables the others, and the whole is more than the sum of its parts.
My name is Stephen Reynolds, and I’m the Industry Principal for Chemicals with AVEVA. I am a chemical engineer and began my career as a unit engineer. I continued my work in operations in a variety of roles ranging from unit engineering to operations management. After 20+ years in industry, I have traded in my steel toes and have begun my own digital transformation.
By luck or by plan, the majority of my career has been spent in operations. Miraculously, I skipped the requisite rotation through project work and instead served as a subject matter expert or approver on a team with its own project manager. I’ve seen good projects and bad projects and some that even delivered on their initial premise. Good projects all have one thing in common–knowing where we are and realizing we’re going somewhere new. Having a vision is one thing, but the path to execution is full of hurdles–project managers call them “gates.”
My plant project work went through the front-end loading (FEL) process. Three gates took us through options, conceptual engineering, and basic engineering. When things got crazy, someone invented an FEL-0 phase, which covered the back-of-the-napkin lunch musings. The goal was to weed out bad projects from good ones and move forward. We captured information and sent it to the next phase, sometimes with a new team. First, we used paper, then digital folders in a shared drive, then SharePoint, and now Microsoft Teams, likelier than not. Documented outputs of each gate that moved forward in the process required both document and change management. We did this manually, which was not without mistakes.
Imagine connecting those dots at the digital level: The initial model informs the conceptual, basic, and final design. Changes made in the model are propagated through the design platform and into final specifications. Assets are defined as part of the digital twin, which carries the reference to these crucial documents. Collaboration occurs globally.
Now, as the project continues, construction and commissioning take place. The models, simulations, and 3D renderings now inform virtual training programs and commissioning walkthroughs. Assets in the digital twin are now paired with real-time process data from automation and control systems. A combined industrial data infrastructure brings the data together and translates it into information that empowers the connected worker.
If you’ve ever engineered a project the “hard” way, I invite you to explore AVEVA’s engineering solutions. Our customers deliver successful projects faster, cheaper, and more error-free–without all the paper.
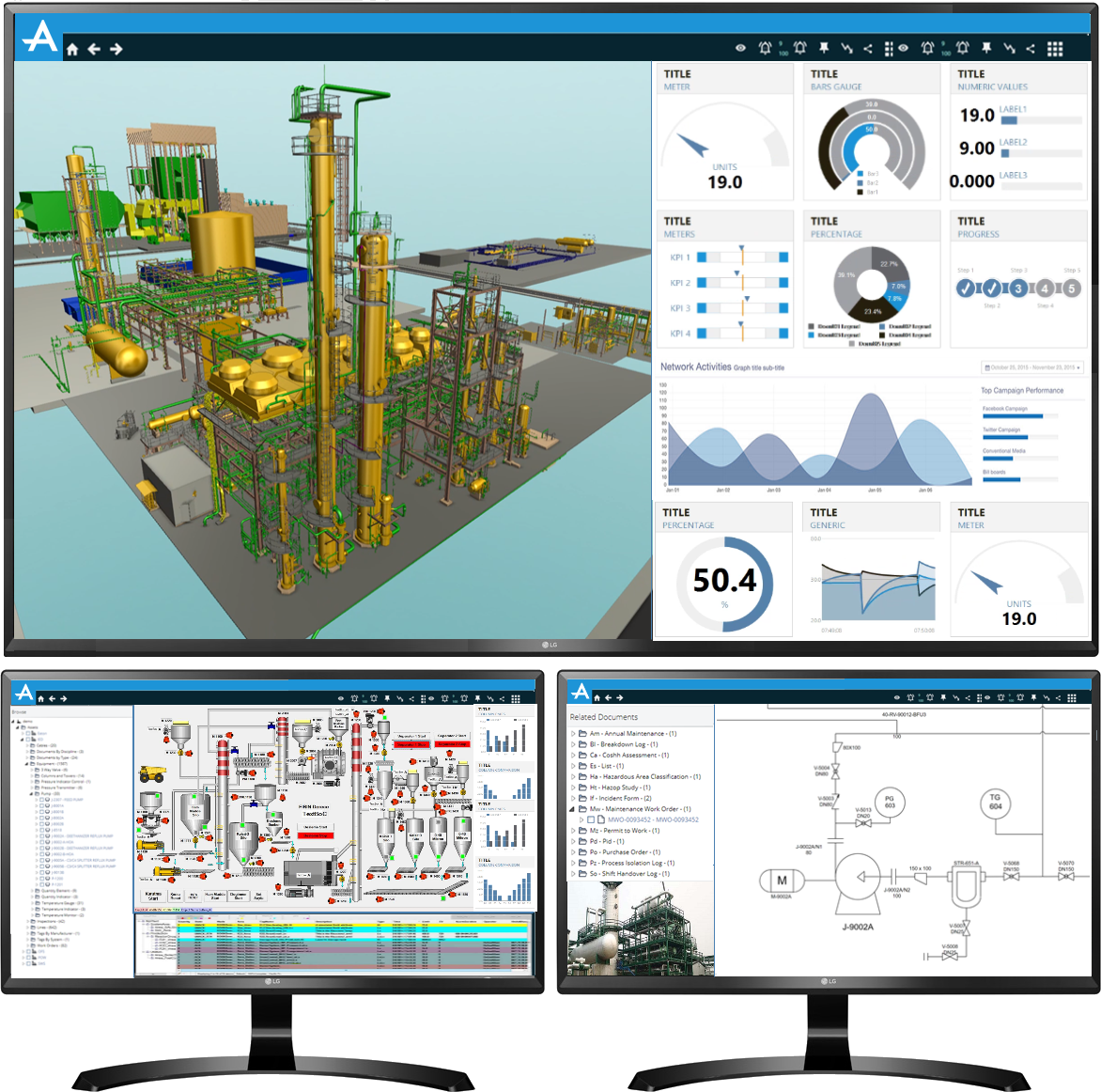