How digital solutions are creating smart mines of the future
Written by Martin Provencher, Global Industry Principal for Mining, Metals and Materials, AVEVA
The last two years have been pivotal for the mining industry. Global economic and environmental pressures have seen owners and their engineering, procurement, and construction (EPC) partners turn to digital technologies to help solve project and operational challenges and operate more sustainably. But there’s more progress yet to be made.
Most mining organizations have already undergone perhaps the most difficult steps toward digitalization—securing buy-in for their digital journey and beginning their transformation. Much like mining engineering teams, new digital tools often work in isolation, unable to share critical information between different applications.
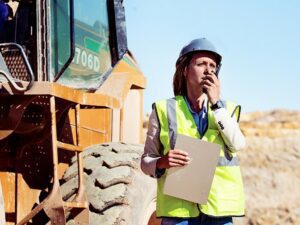
Create the future of smart, safe, and earth-friendly mining
Discover how digital transformation will enable miners to remain sustainable and competitive.
To achieve real value, mining companies must unify their engineering tools, data, people, and processes in an intelligent digital twin in the cloud. This next step in digital transformation will ensure those engineering tools are working hard to transform operational performance and deliver throughout the entire value chain. By aligning everyone around a single hub, the mining sector can address its three most urgent areas of focus: safety, environment, and performance.
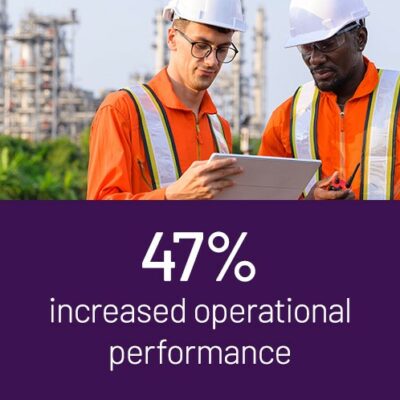
In a recent study of digital innovation in the mining industry, Accenture found that 40% of mining executives have achieved better decision-making processes since introducing digital solutions while 47% cited better operational performance.[i]
Safety
The mining sector takes its commitment to safety seriously and has stringent processes in place to protect its people. One of the most common causes of incidents is human error. Digital twin technology is revolutionizing worker training, while also reducing the number of people needed on site.
It’s estimated that digitalization could save around 1,000 lives and avoid 44,000 injuries globally per year. This equates approximately to a 10% decrease in lives lost and a 20% decrease in injuries in the industry.[i]
Operator Training Simulators (OTS) can be tailored to each mine, using the mine’s digital twin data enhanced with advanced process simulation. With access to a realistic replica of the mine and its operating and control systems, workers have a safe environment in which to practice, experiment, fail, and, most importantly, learn.
For greenfield capital projects, OTS provides operators with the competencies to safely operate a new mine. For brownfield projects, high exposure to simulated scenarios builds confidence and skills. OTS empowers individuals to work more safely and have more effective safety discussions. In operations, cloud OTS deployments enable teams to test scenarios without needing to step foot on site.
OTS built around a mine’s digital twin is a cost-effective way to provide continuous training opportunities to the workforce. Training can be scaled up or down, depending on the project phase, and it can support operational imperatives without the disruption or cost associated with traditional, classroom-based learning. What’s more, this kind of immersive training is significantly more effective for knowledge retention than the one-and-done classroom approach.[ii]
Performance
One of the greatest challenges to improving the performance of capital projects and operations is siloed working. Given the complexity and scale of mines, teams often work in self-governing silos. This leads to reactive decision-making, schedule and cost overruns, information leaks, lost data, wasted resources, high energy consumption, and poor asset utilization.
Connecting engineers to the right tools and data at the right time improves project collaboration, transparency, and decision-making, which maximizes value. With a two-way flow of data at every stage of the lifecycle, companies can become proactive—even predictive—rather than reactive, empowering teams and ensuring a smooth flow of information all the way from pit to port.
One mining company that benefited from digital twin technology in their greenfield project is K + S Potash. The company partnered with AVEVA to streamline its handover process across nine different EPC contractors situated in multiple locations around the globe. Its key objectives were to accelerate time to start and ensure a complete and smooth handover.
To achieve this, the company needed the EPC teams and K+S Potash’s operations leadership to work from consistent data. Read the case study to see how, together, we successfully delivered a unified suite of solutions to ensure the smooth handover of a complete digital twin.
Environment
Every industry is under increased pressure to reduce its environmental impact and demonstrate its commitment to sustainable working. The days of greenwashing are long gone—shareholders, regulators, and the public demand transparent and ongoing efforts to reduce emissions and waste.
Going green is also good for business. According to the World Economic Forum, digitalization could generate a reduction of USD 610M tonnes of CO2 emissions, with an estimated value to society and the environment of USD 30Bn.[iii]
For the mining industry, the pursuit of greater sustainability is no small task. Through intelligent digital twin technology, EPCs and owner-operators can gain end-to-end visibility and control of both their capital projects and operations. With highly visual dashboards and real-time data at their fingertips, project execution teams can minimize wasted resources and materials during the construction phase. Once operational, digital twins make it easier to flag environmental risks and identify opportunities to improve standards.
Unified digital solutions are helping mining companies reduce the complexity of capital projects and operations. Through digitalization, they’re realizing new levels of workforce empowerment and performance optimization across project execution, operations, safety, and sustainability.
Tomorrow’s mines will be connected and intelligent. Workers will be empowered by unrivaled access to trusted data insights and unified tools and processes to make smarter decisions, faster—driving performance, and minimizing impact on the environment and communities where mines are active.
[i] Accenture Study: Digital in Mining: Progress And Opportunity (2017)
[ii] Digital Transformation Initiative Mining and Metals Industry, World Economic Forum (2017)
[iii] http://uir.unisa.ac.za/handle/10500/20676
[iv] https://www.weforum.org/agenda/2019/01/why-digitalization-is-the-key-to-exponential-climate-action/