Digital maturity journeys in manufacturing
Written by Sree Hameed, Senior Industry Marketing Manage, AVEVA
The best part of AVEVA World for me is the customer stories. As the track owner for manufacturing, I spent many weeks vetting the abstracts and reviewing the slides. Yet watching customers on stage and hearing their powerful stories in person was the payoff from all the work of coordinating three days of content across consumer products, life sciences, and general manufacturing segments.
These stories illuminate the diversity and innovation in customers’ journeys toward digital maturity. The different stages can be grouped along four major themes, with many large enterprises often managing multiple initiatives that align with these themes as part of their ongoing multi-site, multi-stage transformation programs.
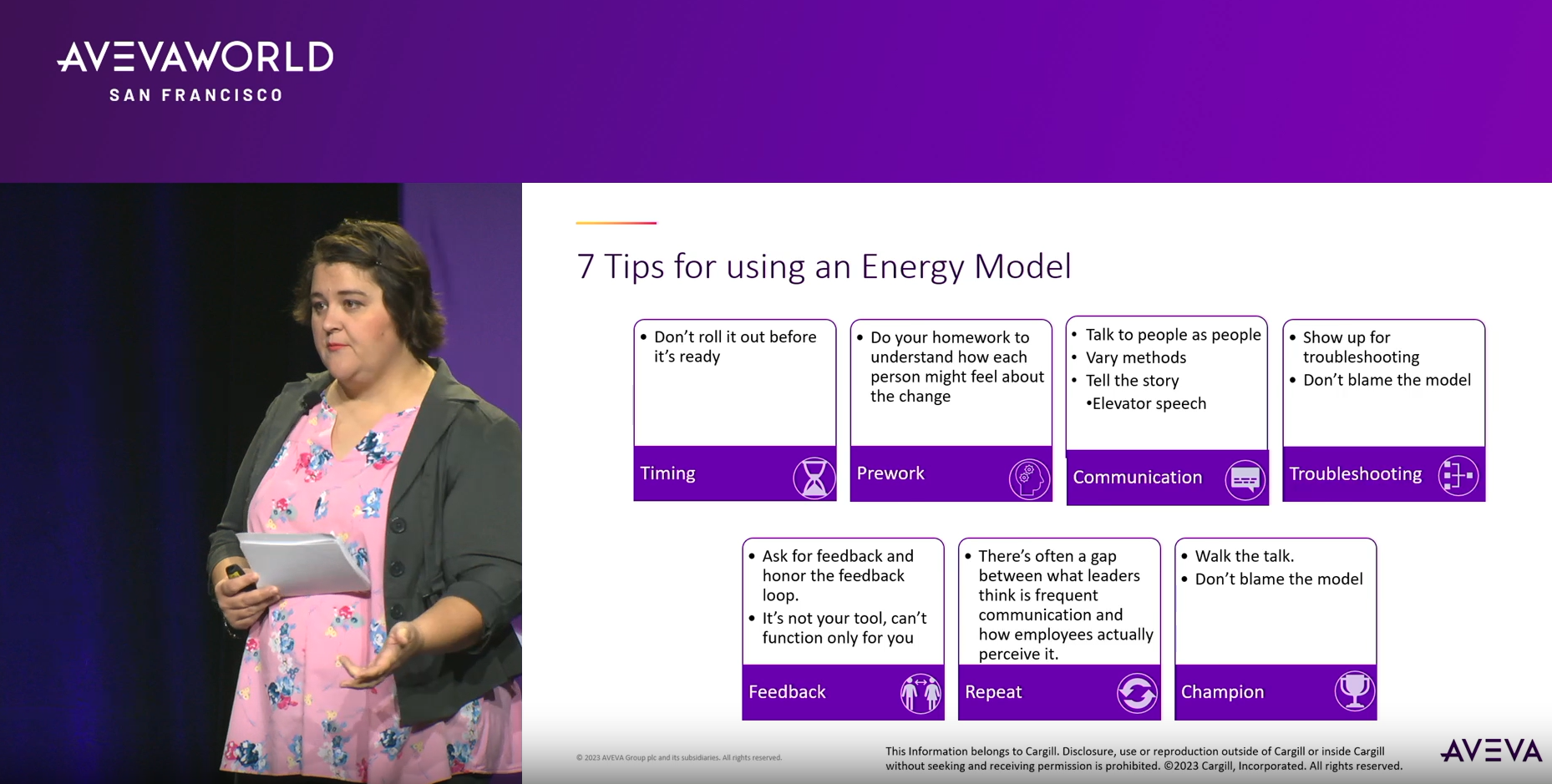
Digitalization of work procedures
These are fundamental first steps in the digital journey, digitizing manual processes as well as finding new ways of working that improve performance.
- Genentech: The Vacaville site sought to extend its proven digital capability for large-scale bioreactor batch management to the previously paper-based batch records of the smaller, lab-scale bioreactors. The project resulted in higher first-time quality as well as annual savings of over $170,000 by eliminating paper tickets.
- SAN-I-PAK World Health Systems: This innovative project involves the management of regulatory data in the treatment and disposal of medical waste. It led to the creation of SAN-I-PAK NET, a portal that provides detailed, real-time data to all stakeholders in the disposal chain including hospitals, clinics, and regulatory agencies.
- Cargill: Using data from AVEVA™ PI System™, the customer team deployed an energy management framework that enabled process engineers to quickly create energy usage models that empowered frontline users and managers to understand and act on energy savings opportunities.
- Vivix Glass: Cloud solutions helped Vivix collaboratively design and build a new factory while minimizing risk in the company’s strategic capital project.
AI and advanced analytics
At this stage, companies are looking to build upon an established data foundation by using analytical models that are more sophisticated, potentially leveraging advanced technologies like AI and machine learning.
- Sanofi: Using the standard data structures from the existing AVEVA PI System investment to digitalize various aspects of their RCM (reliability-centered maintenance) program and using Quartic’s AI to monitor critical failure modes on equipment at the site, Sanofi reduced cost of goods sold and maintenance cost by 25%, among other benefits.
- Maple Leaf Foods: A great example of a company that continues to diligently execute its digital vision since 2016, the heritage site builds upon its existing MES investment to leverage Industry 4.0 technologies like IoT and AI for advanced analytics. Using Braincube for machine learning, the project quickly resulted in a 10-12% increase in gross profit by reducing waste across eight use cases.
- Analytics for Industry: The Energy Monitoring System (EMS) developed by this AVEVA partner is designed to be deployed quickly with a rich array of reports for energy and sustainability improvements. The company saw ROI within 3-4 months, validated by actual customer experiences.
- Sartorius: Using AVEVA PI System data to build sophisticated AI/ML models to manage the “chemometrics” of life sciences applications, this presentation sheds light on the various approaches to AI as well as shared the successes of these approaches at Takeda.
Scaling standards across sites
If making a single plant smarter represents one dimension of change, then transforming a network of plants in a programmatic manner is a different dimension altogether. Success in scaling network-wide transformation involves cross-functional teams, centralization of activities, platforms that enable template or “model-driven” approaches to software life cycle management, multiple projects and work streams organized under a multi-phase program, and so on. They often require a “center of excellence” or “smart factory council” to execute such programs in a coordinated manner across multiple sites.
- Tetra Pak: A long-time customer, Tetra Pak has now adopted the model-driven architecture of AVEVA’s HMI/SCADA/MES stack to develop and offer PlantMaster™—a scalable, templatized solution for plant automation and information management as part of its services portfolio for the food & beverage industry.
- Coromandel: AVEVA PI System is the data foundation for the Coromandel Digital Manufacturing Platform (DCMP), a centralized manufacturing information system with real-time data connectivity and 60 operational systems across multiple sites. Coromandel saw robust savings in predictive maintenance (proactive alerts) and predictive quality (control of nutrient recipe variables).
Industrial ecosystem collaboration
Using flexible, secure, real-time data-sharing tools, organizations are empowered through an ecosystem of applications, partners, and customers to optimize operations and accelerate innovation.
- Biosana Pharma: Using AVEVA™ Data Hub as a cloud data platform to collect data from various sources at the development laboratory and the manufacturing site, Biosana was able to ensure comparability, data integrity, and contextualization.
Together, these successes demonstrate how AVEVA’s broad portfolio and its partners continue to help customers at various stages of maturity in their digital transformation journey.