AUVESY-MDT Article: Taking Command of Data in Increasingly Complex Industrial Operations
FAQ with Gary Gillespie, President of Americas at AUVESY-MDT
Growing numbers of industrial IoT devices and field devices are generating exponentially increasing streams of data to be monitored, processed, managed, and utilized. The resulting complexity is adding to challenges for operations managers and engineers trying to keep up with configuration and version management and backups; software and firmware updates; user authentication; and a lack of visibility across fragmented production environments. This FAQ addresses how to gain better control over industrial asset management.
Why do plant operators need a data management solution for industrial devices?
Growing automation of industrial enterprises creates greater complexity with a multitude of devices that may be subject to human error, machine failure, and cyberattacks. Any of those issues can interrupt production, resulting in reduced revenue, increased costs, and lost profits, along with disappointed customers who may be prompted to turn elsewhere for more dependable suppliers. Data management solutions to this point have only covered individual machines or partial aspects of a plant, such as PLC, SCADA, and HMI. So, operators and engineers have only partial visibility into the status of ongoing operations. To see a list of devices supported by the data management solution octoplant, go to the Device Finder tool.
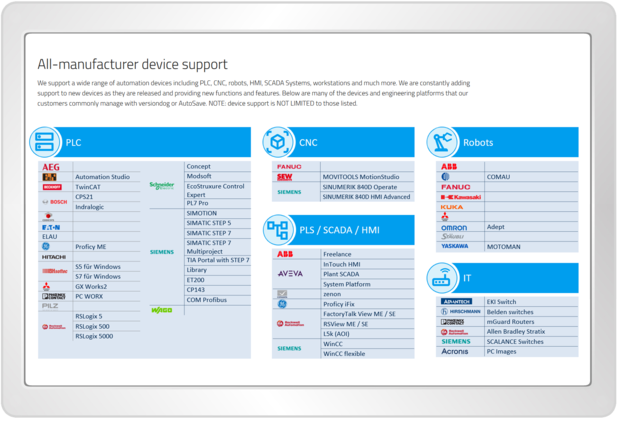
Will industrial data management overlap and duplicate what companies are investing in IT?
IT and OT have developed along separate paths and the growing reliance on automation and digitization is exposing the weaknesses of industrial data management. IT has made great strides in improving the availability and useability of diverse data sets, while OT has lagged in digital asset management. Version control, automatic backup and restore, and visibility into plant operations tend to rely on a hodgepodge of device- or vendor-specific solutions providing a fragmented management environment and an inability to fully realize the benefits of data analytics to guarantee better, safer, and faster decision-making.
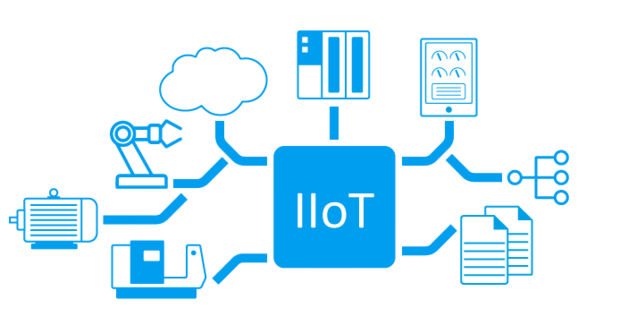
What are the essential elements of an industrial data management solution?
Managing software, firmware, and configuration settings in a standardized manner is a foundational element of modern plant operations. Being able to connect to all commonly found automated production and IoT devices is the only way to keep track of program updates and comprehensively manage version control. Too often, when a device fails, operators back up control programs from outdated or improper versions and control settings. This can extend the duration of downtime and result in incorrect production that ends up having to be scrapped or remediated.
What else can a data management platform accomplish?
With complete version management, plant operators always have access to the latest version of software or firmware and can see whether changes are required. With the ability to automate backups across the plant, operators are able to save time and labor, reduce errors, and ensure a reliable data snapshot of the entire production environment. An easy-to-use data management platform will unlock valuable business intelligence capabilities by consolidating and analyzing complex, fragmented production environments. Better industrial data management enables companies to increase overall equipment effectiveness by digitally connecting information from field, control, supervisory, and enterprise levels. They can gain insight into how efficiently components are being used and how frequently changes to specific components are being made. Furthermore, they’ll be able to adopt guidelines and best practices for assets and configuration settings data that can lead to an increased level of standardization and efficiency.
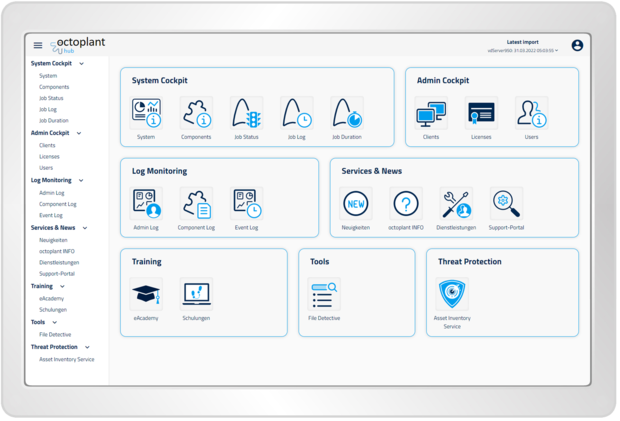
How will a data management platform improve compliance?
Compliance management is only growing in importance due to fast-changing regulatory mandates such as the KRITIS IT security law, the FDA 21 CFR Part 11 regulation, and GxP rules to ensure process quality, production documentation, and proof of compliance. Integrated documentation and regulatory workflows, such as those for the release process, help ensure reliable and seamless compliance management in which risks are reduced resulting in rule-compliant, traceable, and auditable production processes.
How does plant data management impact cybersecurity?
In today’s environment, everything is networked, or will be soon. Cybercriminals are relentless in finding network connections that operators may not even be aware of, creating more opportunities for damaging security breaches that can result in theft of intellectual property, ransomware, and cyber vandalism. Ransomware can be devastating, bringing operations to a halt until the plant owner agrees to pay an attacker, typically in hard-to-trace cryptocurrency. With an effective data management platform, operators can ensure they have addressed security vulnerabilities to protect production environments from attack, prevent damage, and avoid downtime. The ability to quickly restore production environments and devices to pre-attack versions increases resiliency in the face of unknown threats.
Decision-makers must balance competing demands for resources. Why should data management get a higher priority?
In this digital era, data has been labeled the new gold. It holds the ability to create value when organizations can consistently evaluate data and unlock insights that can be used to make better, safer, and faster decisions to increase plant productivity. Plant environments are only going to become increasingly complex with more Industrial IoT devices, robots, and automation. Data management in those environments is essential to simplify that complexity so organizations are more resilient, agile, and profitable.