A digital thread: What it is and why you need it
Written by Jeremy Wilbert, Sr. Product Marketing Manager, AVEVA
Digital thread is one of the latest buzzwords you’ve seen floating around. But it’s not just some meaningless marketing jargon. It expresses the simple, powerful function of what’s otherwise very complex technology.
Simply put, a digital thread is the digital flow of data and information about something, chained between several connected points and made accessible to users. Those connected points can be systems, devices, or people—but they’re all bound together by the same continuous thread of information. While the underlying technology that creates a digital thread is complicated, its function is straightforward: get the right information to the right people.
Most industrial organizations have the beginnings of a full digital thread already, even if they may not realize it. Various systems like HMI/SCADA and historians, among other tools, already help get information where it’s needed and format it in a way that’s most useful.
In the industrial process space, a digital thread often links detailed information about the process from the equipment to other areas of the operation and business. The continuity of the information means it can always be tied back to its source and the information one group accesses is the same information another group accesses. It gives everyone across the organization trust and confidence that the data they’re using to make decisions is reliable, accurate, and timely
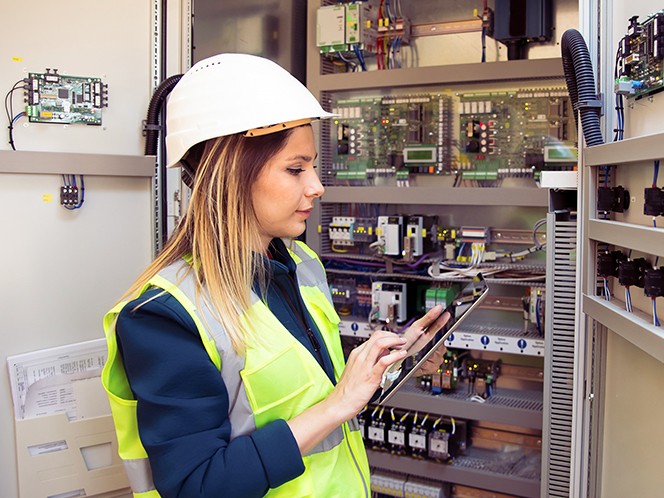
Why do you need a digital thread?
People make decisions at every level of industrial organizations. For those decisions to have their intended outcomes, they have to be fed with the best data and information available. At face value, that’s a pretty basic observation—until you start to think about how all those different decisions require different kinds of information. Take a look at a simple example.
For a process control engineer, the granular trend of temperature, pressure, flow, and electrical current over the last hour may be enough to make an initial assessment of whether a piece of equipment is performing as expected. That assessment will help decide if it needs to be taken out of service for repair to avoid critical damage, as well as help other people make decisions specific to their roles and particular perspectives on the process.
The control room manager who is responsible for meeting the daily targets needs to know how the whole facility is operating and whether she needs to make adjustments to meet those targets. She may need a more aggregated form of information about the equipment’s performance: Is it steady, or trending down? What’s the process control engineer’s decision for repair? What similar assessments have others made about additional process lines or trains?
All that information will help her determine the impact of equipment performance on the facility as a whole and how she should adjust to balance daily targets against overall process health. She may use more information than the process control engineer, but in a more simplified form.
An executive located in another geographic location may observe how the facility is performing at an even higher level of aggregation—built from the same raw data the process control engineer sees, but transformed into a series of different metrics leveraging other information. The executive uses that information to determine whether they need to shift production to another facility to meet customer demands for the month, what the cost of that shift might be, and other broader impacts it will have.
At the heart of this simple example is a digital thread of data and information that winds throughout the organization—at both different time scales and levels of aggregation—to inform decisions, supplemented by adjacent details relevant to the decision. That digital thread enables people throughout the organization to make faster and better-informed decisions because the information is readily available, pre-formulated for what they need, and based on the underlying information from relevant sources. Without a digital thread, decision-makers may not be able to trust the timeliness and accuracy of everyone’s responses.
How to get started with your own digital thread
A good place to get started is the process facility itself, as much of the higher-level decisions will ultimately depend on data generated from the base temperatures, pressures, and flows of any industrial organization. Creating a digital thread around the short-term requirements of the process will build value upward as you aggregate data into other systems.
Begin by ensuring that:
- The process control system is effective and reliable.
- Operators have the information they need, even if they didn’t know they needed it.
- A historian captures data securely, to help facilitate trust.
- Users can readily access analytics on any device and at any location.
How you link these systems, devices, and people in a digital thread will depend on your organization’s goals and resources. You’ll need to ask:
- Where does the data or information originate?
- Where does it get stored?
- Who needs access to the data or information?
- How will they access it?
- What form do they need to see it in?
- What other information will be valuable to have alongside information from your digital thread?
- Where else does information need to go?
Achieving a full digital thread in one project is likely impossible, but you can assemble smaller pieces of the overall chain over time and create increasingly greater opportunities to tune the outcomes in preparation for the next piece.